Industrial Wastewater Management
Ensure cost efficient compliance of environmental effluent with reliable instruments
Effluent limits
Environmental regulatory agencies all over the world have established effluent limits for defined substance classes that can be present in wastewater depending on its origin. Besides organic substances causing problematic oxygen depletion in the receiving water body, nitrogen and phosphorous need to be tightly controlled as they are the primary cause for excessive algae growth. In industrial wastewater, additional parameters like heavy metals, defined chemical components or simply effluent color need to be closely monitored as well, depending on the specific nature and origin of the wastewater.
Real-time monitoring of BOD content of wastewater streams allows the plant opportunities to reduce municipal treatment costs, increase process efficiency and lower operating expenses.
Organic carbon
The most important parameter however is the amount of organic carbon present in the sewage. Traditionally this is determined by measuring the so-called Biochemical Oxygen Demand (BOD), which is a measure of the amount of biologically degradable substances in sewage. These substances are broken down by microorganisms; therefore, oxygen demand is measured in terms of the oxygen consumed by the microorganisms over a period of five days (BOD5) or seven days (BOD7). In the US, the Environmental Protection Agency (EPA), which establishes guidelines as required by the Federal Water Pollution Control Act, uses BOD levels to measure an industrial plant’s effluent strength. It is incumbent for a plant’s effective wastewater treatment program to effectively monitor BOD content of their wastewater before sending it to sewer.
How do you measure the carbon load in real time?
While BOD monitoring is the method most closely reflecting biological reality, the parameter cannot be used as a real-time indicator to control wastewater streams due to its long lead time of five or seven days. Therefore other parameters that can be measured in real time reflecting the organic carbon load have to be used for control purposes. Depending on the prevalent nature of the organic load, different sensors can be utilized. If the organic load comes as undissolved solids or a suspension (e.g., dairy products), it can be detected and measured using optek’s near infrared (NIR) sensors AS16-N, AF16-N or TF16-N turbidity meter. Dissolved organics are classically reflected by the Spectral Absorption Coefficient (SAC) measured at 254 nm, using a UV-sensor such as the AF45.
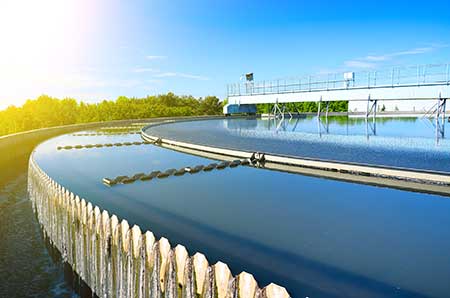
Final clarifier in a wastewater treatment facility
Products used to monitor wastewater
Sources of organic carbon in industrial processes
High levels of organic carbon are typically a direct indicator of product losses during production. Besides damaged equipment like broken heat exchangers where product can leak into cooling water, insufficiently controlled cleaning and sterilization processes (CIP/SIP) and suboptimal product interface detection are the main reason for product losses and high organic loads in the resulting wastewater stream.
Product interface detection
To tightly control product handling, a reliable detection of the product is necessary. The ability to differentiate between products and the water used for moving the products directly minimizes the amount of product that is flushed into the waste stream. Depending on the physicochemical nature of the product, different sensors can be applied. In dairy applications, turbidity sensors like the AS16-N or AF16-N can be used; whereas in the beverage industry mostly color sensors like the AF26 or the AF16-F are used.
Clean-in place (CIP) and sterilization in place (SIP) monitoring
Besides achieving the primary objectives of CIP/SIP processes such as cleaning and sterilization, proper monitoring of said processes has several advantages, such as minimizing energy, water, and cleaning agent consumption. The amount of residue and debris in the cleaning water stream can be monitored using a turbidity sensor like the TF16-N to avoid over-cleaning. In case acidic or caustic agents are used for cleaning and/or sterilization, a reliable broad range conductivity sensor like the ACS60 or ACF60 can be used to determine the concentration of the cleaning agent down to the conductivity level of ultra-pure water used to rinse the system afterwards. By doing that, agent solutions which are sufficiently clean can be recycled and the amount of pure water for cleaning is likewise minimized. Minimizing the use of cleaning agents not only lessens their consumption, but also lessens the load of cleaning agents sent to the wastewater stream. Cleaning agent excess can negatively impact the wastewater treatment process because their biocidal properties or extreme pH values reduce the microbial population in the biological treatment.
Color monitoring
While color monitoring of raw water for industrial or drinking water purposes is relatively common, especially when a natural water source is used, color monitoring of wastewater plant effluent is usually limited to “color intensive” industries like textile or leather manufacturing plants. To ensure colorless effluent wastewater quality, the VIS absorption sensors AF16-F or AF26 can be used for real-time color monitoring.
Benefits of monitoring
While the benefits of reduced product loss is evident, describing the advantages of controlling the organic load in the effluent stream needs more differentiation. In case the plant has its own wastewater treatment facility, the measured load can be used to directly control treatment parameters such as the aeration intensity. In case the industrial wastewater is treated in a municipal plant, they will usually use organic carbon loads to determine charges for industrial users of their wastewater treatment facilities. In addition, there are load limits that the industrial plant is allowed to discharge at a given time to avoid overloading the treatment plant. Breaching those limits can result in substantial penalty payments. With no reagents needed for the analysis, the total cost of ownership for the above mentioned sensors is very low, allowing for a short return-on-investment period based on reduced product-loss and lower water usage.
Get in Touch with optek
If you have any further questions or queries please do not hesitate to get in touch.