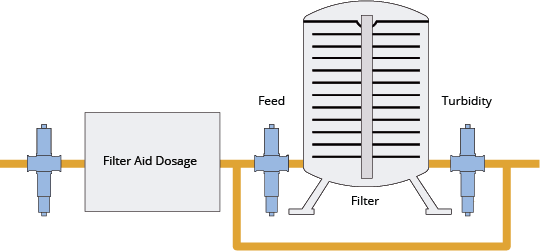
Filter Control
Many processes require filtration to clarify the product. Filtration proceeds from coarse filtration by means of separators, decanters, or settling tanks to a final polishing by diatomaceous earth (DE) or other precoat media filters.
To control product clarity, a turbidimeter can be installed at the start of the filtration process and in between each filtering step. If product turbidity reaches an unacceptable level, the flow can be automatically recirculated or switched to an alternate filter.
optek Products used in Filter Control
Effective Filtration
optek photometers can monitor and control filter media dosing to ensure uniform precoat feed. This reduces filter media usage and extends the filter run by dosing only the amount of media necessary for effective filtration. Excessive amounts of filter media reduce the effective filtration time and increase product losses and process downtime.
The use of optek inline sensors greatly reduces the risk of equipment failure and operator error. This avoids costly refiltering, downtime and poor product quality. optek sensors ensure that proper clarity is achieved before transferring the product to the next process stage.
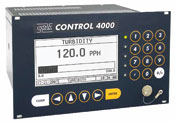
optek C4000 Photometric Converter
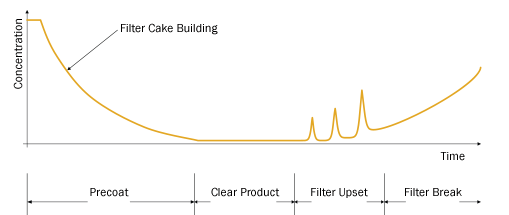
Feed Stream
In addition to filtrate monitors, many large-scale processors implement an AF16-N NIR absorption sensor on the precoat side of the filter. This NIR turbidimeter measures total suspended solids in real-time allowing operators to control filter media dosing based on need rather than flow rate. Continuous monitoring of filter media addition allows accurate control of precoat concentration to ensure proper cake thickness and uniformity. This optimizes the use of filter media while extending filter runs. As the precoat media is deposited, filtrate clears up gradually. The moment the sensor detects the filtrate has achieved acceptable clarity, the converter signals the filter controller to switch from precoating to filtering operation.
The AF16-N sensor is also used to detect heavy solids carryover from storage tanks or prefiltration failure. Upon reaching the user defined high turbidity level, the filter can be switched to a recycle mode and incoming product is diverted to a settling tank, separator or to be refiltered. This will prevent filter blinding and provide extended use of the filter.
Backwash Optimization
An inline sensor can also be used to optimize filter backwash process by measuring the turbidity in the water, saving time, energy and water usage.
Filtrate Stream
To ensure product quality, it is necessary to measure and control turbidity at the filter outlet. An optek TF16-N scattered light turbidimeter precisely monitors very low concentrations of suspended solids from 0 – 0.5 to 0 – 500 PPM or 0 – 0.2 to 0 – 200 FTU to achieve the desired clarity of the product.
Installing an inline turbidimeter on the filtrate stream allows for the automatic diversion of the filtrate to recirculate until the product clarity is improved to an acceptable level.
Installed directly inline, optek turbidimeters optimize filter performance and immediately detect filter upsets or breaks. These turbidimeters also greatly reduce or eliminate the amount of sampling and lab analysis performed for quality assurance.
Quality Control
Proven to be a valuable tool for process control and quality assurance, optek turbidimeters ensure that product clarity is consistently maintained. Reducing product losses, increasing filtration capacity and optimizing filter media are only a few of the benefits optek inline sensors provide.
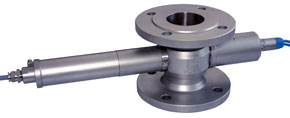
optek TF16-EX-N Scattered Light Dual Channel Turbidity Sensor
Get in Touch with optek
If you have any further questions or queries please do not hesitate to get in touch.