Conductivity Measurements
The specific electrical conductivity σ [S/m] is a physical parameter describing the ability of a substance (liquids, metals, gases) to conduct electrical current. In liquids, the electrical conductivity is caused by positive and negative charged ions that are able to interact with an applied electrical field. In general, the conductivity is dependent on the concentration and type of ions, and the temperature.
There are two technical approaches to measure conductivity - inductive and contacting.
Inductive Conductivity
Inductive sensors are using two electromagnetic coils usually encased in a polymer ring. An alternating voltage is applied to the driving coil, which induces a voltage in the receiving coil. The induced current is influenced by the conductance of the solution. Due to the sealed casing, inductive sensors can be used in aggressive environments, but they are not suited for conductivities below 15 µS/cm.
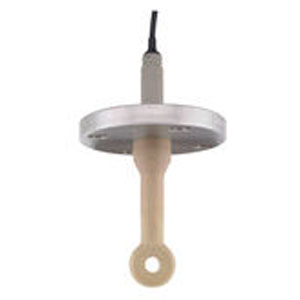
An example of an inductive conductivity sensor
Contacting Conductivity
Contacting sensors consist of conducting electrodes being in direct contact with the medium. The primary parameters measured are voltage and the applied current. The interdependence of both parameters, described by Ohm’s law, allows for the calculation of a resistance R (measured in Ohm [Ω]) or the inverse – the conductance G (measured in Siemens [S]).
Multiplying the measured conductance by the cell constant corrects for the individual properties of the sensor. The result is the conductivity σ, which only depends on properties of the solution.
Typically, the cell constant is determined in the factory and entered into the associated conductivity meter or converter. To achieve the highest possible accuracy it is recommended to calibrate the system when installed in the process using a calibration solution having a nominal conductivity within the desired measurement range and temperature.
The conductivity scale
Between the standard unit “S Siemens” (100) and the mostly used unit “µS micro Siemens” (10-6) there is a difference of 106 = 100.000. If a conductivity sensor measures from µS up to mS (milli Siemens 10-3) up to S, it is obvious that the sensor performance cannot be the same over the whole range. That is why conductivity sensors have their accuracy linked to the measuring range.
Typical conductivity values at 25 °C (77 °F) | |
High purity water | 0.05 μS/cm |
Tap water | 500 μS/cm |
Acetic acid 10% | 1.76 mS/cm |
NaOH 10% | 353 mS/cm |