
Crude Distillation Unit (CDU) Monitoring
The quality of fractions from the crude distillation unit (CDU) need to be continuously monitored. By installing an optek inline photometer, the refinery maintains peak performance from the column and controls product quality downstream.
optek Products used in Crude Distillation Unit (CDU) Monitoring
Naphtha, gasoline, kerosene and jet fuels are the lightest and highest quality hydrocarbons drawn off the top of the distillation column. Because of their low levels of impurities, they normally have a clear visual appearance. Their color is measured using the Saybolt color scale, where acceptable product quality typically measures between +27 to +30 Saybolt. optek’s strength here is the ability to customize systems to our customers’ requirements. This is accomplished by using application specific wavelengths and OPL’s (optical path lengths) to ensure the best possible resolution for the application.
Heating oils, gas oils and lubricating oils are heavier hydrocarbons that are darker in appearance and drawn from the middle of the distillation column. Their color is measured using the ASTM color scale, ranging from brightest 0 to darkest 8, where acceptable product quality typically measures between 2 to 5. Using an optek AF26 sensor in conjunction with the C4000 converter, the refinery operator can continuously monitor the color of any refined hydrocarbon in any color scale. This allows for real-time determination of process upsets, short term peaks or inconsistencies can be controlled (e.g., by diverting ‘’out of spec’’ diesel to storage or buffer tanks until it can be mixed with a higher quality diesel) preventing loss of product while maximizing process efficiency.
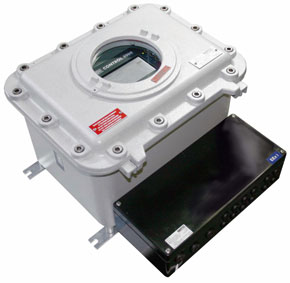
Flameproof housing EX d for optek C4000 converter
Contamination Detection
Increased color intensity typically indicates the presence of undesirable contamination resulting from a process upset or a reduction in process efficiency. Upsets generally occur when the heavier hydrocarbon fractions, such as crude, are carried upward with the lighter fractions, resulting in their contamination. If not detected immediately, the contaminated product will feed downstream, damaging plant equipment and reducing CDU efficiencies.
Get in Touch with optek
If you have any further questions or queries please do not hesitate to get in touch.