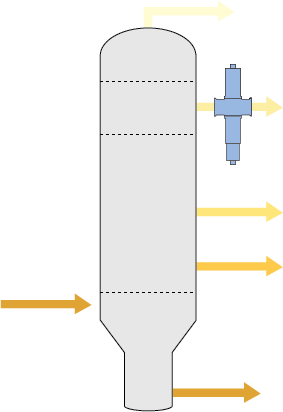
Color of Refined Fuels
The petroleum refining and petrochemical industries benefit greatly with the use of inline color measurements. Detecting color changes directly in the process stream alerts refinery personnel of immediate process upsets that may affect final product quality.
optek Products used in Monitoring Refined Fuel Color
Typical Applications
- Detect crude carryover in refined product cuts off the CDU (crude distillation unit)
- Verify sulphur removal efficiency at diesel fuel desulphurization units
- Product quality / color verification at NGL (natural gas liquids) custody transfer points
- Product quality / color verification at lube oil processing plants
- Product quality / color verification of refined fuels after final processing / before sale
Historically, monitoring color changes was accomplished with a “grab sampling” technique and/or relied on human interpretation comparing samples against ASTM, Saybolt, or other color standards. Today, these measurements are done with precise and reliable inline color sensors from optek.
Refined Hydrocarbons and Color Scales
The petroleum refining and petrochemical industries rely on Saybolt and ASTM color scales (among others) to quantify product quality. ASTM D1500 defines the ASTM color scale (0.0 to 8.0 ASTM) and is used for determining the color of lube oils, heating oils and diesel fuel oils. Product with a faint color below 0.5 ASTM are often defined by the Saybolt color scale. ASTM D156 defines the Saybolt color scale (+30 to -16 Saybolt), and is used for determining the color of gasoline, jet fuel, kerosene, naphtha and NGL.
Typical Color of Refined Fuels Measuring Ranges:
- +20 to +30 Saybolt - Naphtha, Gasoline, Jet Fuel, Lt Diesel
- 0 - 5 ASTM - Heavy Diesel, LVGO, HVGO, Lt Lube Oils
Fuel Contaminant Monitoring
Often, color changes are a signal for contaminations in fuels. Detecting these contaminants directly inline allows operators to redirect the process for further refining or redistillation.
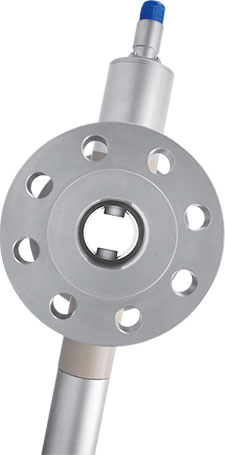
optek AF26-EX-HT-VB Dual Channel Absorption Sensor
Dual Channel Color Measurement
optek AF26 dual channel sensors compensate for background turbidity or other media constituents automatically using a secondary wavelength. The primary wavelength usually detects color and background turbidity, whereas the secondary wavelength only detects background turbidity or other media constituents. Subtracting the absorption signal of the reference channel from the primary channel gives a compensated signal that is then correlated to any color scale, independent of background interference. Additionally, the reference channel of the AF26 can be monitored independently and outputted as a 4-20 mA signal, allowing operators to gain real-time knowledge of turbidity upsets.
Continuous Monitoring
By installing an optek inline color sensor, the product streams can be continuously monitored in real-time. The AF26 explosion proof sensor will immediately detect color changes caused by upsets or gradual reduction in process efficiency. Even at high pressures and temperatures, these important color measurements are made without the need for sample conditioning.
Get in Touch with optek
If you have any further questions or queries please do not hesitate to get in touch.